High Frequency Welder: Investing in Our Future
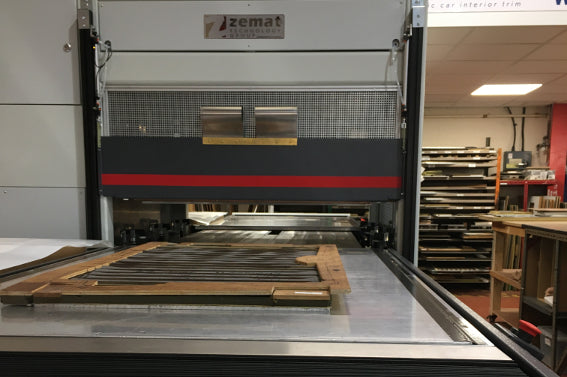
This year has been a time of reflection upon our last 40 years and our development of our product range across the last four decades from Morris Minor to Mini, Triumph to VW, has been reliant upon our investment in our high frequency welding machine. This has allowed us to make a range of classic car interior trim in the original way, and combined with our quality craftmanship and original materials has placed Newton Commercial as the industry leader in manufacturing reproduction interior trim.


With the importance of this process integral to our business, this Autumn we have invested in a brand new high frequency welding machine. Our original machine was installed in the factory in 1988 and has been manufacturing a wide range of products from seat covers to door panels over the last three decades. Our new high frequency welding machine allows us to use the expertise of our skilled machine operator with a brand new piece of kit that is fully programmable, and has two trays to load from both sides of the machine for greater efficiency. We can use the same tooling that we have invested in over the last 30 years to create the same great interior products to the same quality synonymous with the Newton Commercial name.
High frequency welding became an integral manufacturing process to the classic car industry in the 1960's and 70's and allowed patterns such as those on the MKI Mini Cooper door panels to be made with greater accuracy and as high frequency welded patterns became more complex and allowed British classic manufacturers to create a number of iconic designs from the Mini, to the MGB, to the Sprite and Midget ranges from panels to seat covers. Seat covers were made with a simulated stitch, meaning iconic designs could be made with less labour time.

Our investment in brand new machinery is an important part of our commitment to continue to provide original style classic car upholstery for a range of British and European classics and compliments our work with British Motor Heritage. With the help of the European regional development funds we have been able to invest in the future of Newton Commercial, with better improved machinery from our new high frequency welder to our Bullmer CNC cutter. For more details on how Newton Commercial might be able to support your next project please get in touch with our sales team.
Comments on this post (0)